What is Continuous Improvement? Training Included.
Continuous improvement is a philosophy or training approach that seeks to identify and eliminate waste, variability, and inefficiency in all processes, resulting in a steady and incremental improvement in quality, productivity, and customer satisfaction.
There are several methodologies or frameworks that organizations can use to implement continuous improvement, including:
- Kaizen: Kaizen is a Japanese term that means “improvement.” It is a philosophy that focuses on continuous small improvements in all aspects of an organization, from the production process to the way work is done. The goal of Kaizen is to eliminate waste, improve efficiency, and increase customer satisfaction.
- Lean manufacturing: Lean manufacturing is a production approach that focuses on maximizing value and minimizing waste. It is based on the idea of continuous improvement, and involves identifying and eliminating non-value-adding activities in the production process.
- Six Sigma: Six Sigma is a methodology that uses data and statistical analysis to identify and eliminate defects in processes. It aims to improve the quality of products and services by identifying and eliminating the root causes of defects and variability in processes. Six Sigma uses a set of tools and techniques, such as the DMAIC (Define, Measure, Analyze, Improve, and Control) methodology, to drive continuous improvement.
Advantages and Disadvantages of Continuous Improvement
Some advantages of continuous improvement include:
- Improved quality: Continuous improvement efforts aim to eliminate defects and variability in processes, which can result in improved product or service quality.
- Increased efficiency: By identifying and eliminating waste and inefficiency, continuous improvement can help organizations operate more efficiently and reduce costs.
- Improved customer satisfaction: Continuous improvement efforts that focus on meeting customer needs and expectations can lead to increased customer satisfaction.
- Increased competitiveness: Organizations that are able to continuously improve their processes and products are often more competitive in their markets.
- Improved employee engagement: Involving employees in continuous improvement efforts can increase their ownership and commitment to their work, leading to increased engagement and satisfaction.
Some disadvantages of continuous improvement include:
- Resource intensity: Implementing continuous improvement initiatives can require significant resources, including time, money, and training.
- Resistance to change: Some employees may resist change, particularly if they are comfortable with the way things are currently done.
- Short-term focus: Continuous improvement efforts can sometimes be focused on short-term gains, rather than long-term strategic goals.
- Risk of failure: There is always a risk that continuous improvement initiatives will not produce the desired results.
- Limited scope: Continuous improvement efforts may only focus on specific processes or areas of the organization, rather than the organization as a whole.
Cost Savings: Continuous Improvement
Continuous improvement efforts can lead to cost savings in a number of ways:
- Reducing waste: By identifying and eliminating waste in processes, organizations can reduce the use of unnecessary resources, such as materials, energy, and labor.
- Increasing efficiency: By streamlining processes and eliminating inefficiencies, organizations can reduce the time and resources needed to complete tasks, leading to cost savings.
- Reducing defects: By identifying and eliminating defects in products or services, organizations can reduce rework and the costs associated with correcting mistakes.
- Improving asset utilization: By improving the utilization of equipment and other assets, organizations can reduce the need for additional investment in new assets, leading to cost savings.
- Reducing lead times: By reducing the time it takes to complete tasks and deliver products or services, organizations can reduce inventory and carrying costs, leading to cost savings.
- Improving supplier relationships: By working closely with suppliers to identify and eliminate waste and inefficiencies, organizations can reduce costs associated with purchasing materials and components.
Continuous Improvement Quotes
- “The message of the Kaizen strategy is that not a day should go by without some kind of improvement being made somewhere in the company.” ~Masaaki Imai
- “All we are doing is looking at the timeline from the moment a customer gives us an order to the point we collect the cash. And we are reducing that timeline in the value stream by removing non value-added wastes.” ~Taiichi Ohno
- “The world we have created is a product of our thinking; it cannot be changed without changing our thinking.” ~Albert Einstein
- “A corporation is a living organism; it has to continue to shed its skin. Methods have to change. Focus has to change. Values have to change. The sum total of those changes is transformation.” ~Andrew Grove, former CEO of Intel.
- “Good is the enemy of great. That’s why so few things become great.” ~James C. Collins
- “Long-term commitment to new learning and new philosophy is required of any management that seeks transformation. The timid and the fainthearted, and the people that expect quick results, are doomed to disappointment.” ~W. Edwards Deming
- “I’m proud to be Japanese and I wanted my country to succeed. I believed my system was a way that could help us become a modern industrial nation. That is why I had no problem with sharing it with other Japanese companies, even my biggest competitors.” ~Taiichi Ohno
- “Great job. Now make it even better.” ~Dave Waters
- “Many people think that Lean is about cutting heads, reducing the work force or cutting inventory. Lean is really a growth strategy. It is about gaining market share and being prepared to enter in or create new markets.” ~Ernie Smith
- “Improvement usually means doing something that we have never done before.” ~Shigeo Shingo
- “Everything can be improved.” ~Clarence W. Barron
Continuous Improvement Training
Continuous improvement training should be part of every organization. Below you will find training on Lean, Kaizen, Six Sigma and everything else we could find about continuous improvement. If you are new to continuous improvement and looking for a company to research we recommend Toyota. Toyota is known for its quality and just as importantly there is a great deal of available information. If you are looking for people to research on this topic you may want to start with Taiichi Ohno and W. Edwards Deming.
Some people are engrained in a specific continuous improvement philosophy. That is perfectly ok. Cultures play a big part in continuous improvement and how to go about it. This Bruce Lee quote goes well with continuous improvement: “Absorb what is useful, discard what is useless and add what is specifically your own.” The reason I bring this up is because 20+ years ago I worked with Walmart Logistics. We were always looking for ways to improve at Walmart. People were constantly asked “How can we get better today?” When people had suggestion they were either implemented or explained why they weren’t done. Not until later did I find out the same concepts in Lean and Kaizen are what I learned at Walmart. The main thing with continuous improvement is to get started. Ask the people doing the work how to improve and you will be amazed at the responses you get.
Learning Resources
- Best Continuous Improvement Quotes.
- Continuous Improvement Tools: Lean and Six Sigma.
- Deming’s 14 Points on Total Quality Management – TQM.
- Future Manufacturing: Toyota Innovation, Robotics, Artificial Intelligence.
- Great Collection of Quotes about the Toyota Production System.
- History of Continuous Improvement & Quality Gurus.
- How Toyota Changed Manufacturing – Lean Thinking,
- John Shook Explains the Lean Transformation Model.
- Kaizen – Toyota.
- Kanban explained in 60 seconds.
- Lean Manufacturing – Lean Factory Tour.
- Lean Six Sigma In 8 Minutes.
- Process Improvement Quotes and Blogs.
- Process Improvement: Six Sigma & Kaizen Methodologies.
- Pull Systems: Lean Manufacturing
- Six Sigma In Plain English.
- The Path to Success with Paul Akers: Lean Manufacturing
- Toyota Production Documentary – Toyota Manufacturing Production.
- Toyota Supply Chain Management.
- TPS: Kanban Production
Toyota Production System Jidoka: Stopping Production, a Call Button and Andon.
The Best Continuous Improvement Quotes
What is Just in Time (JIT): Smartest Production System in The World
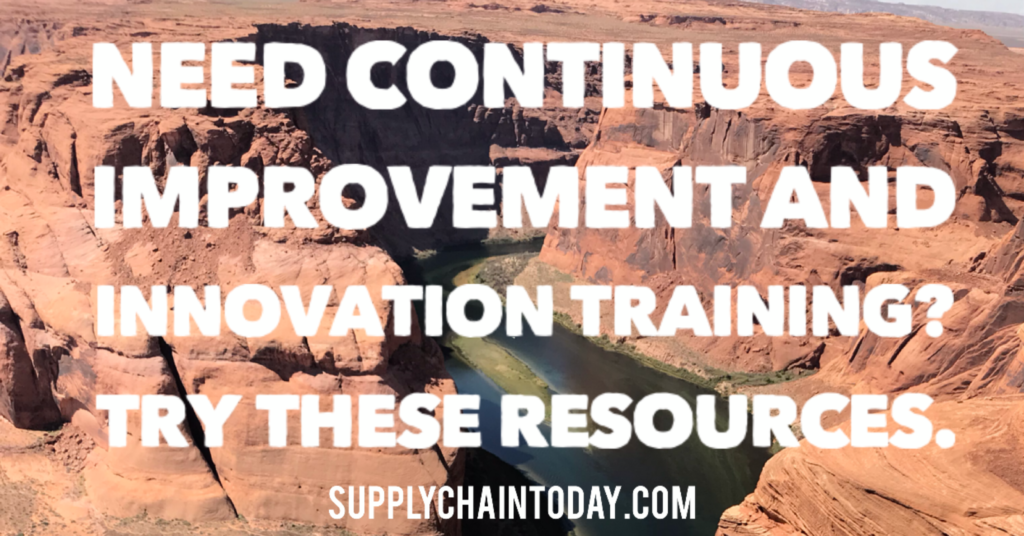
“No idea is so outlandish that it should not be considered.” ~Winston Churchill
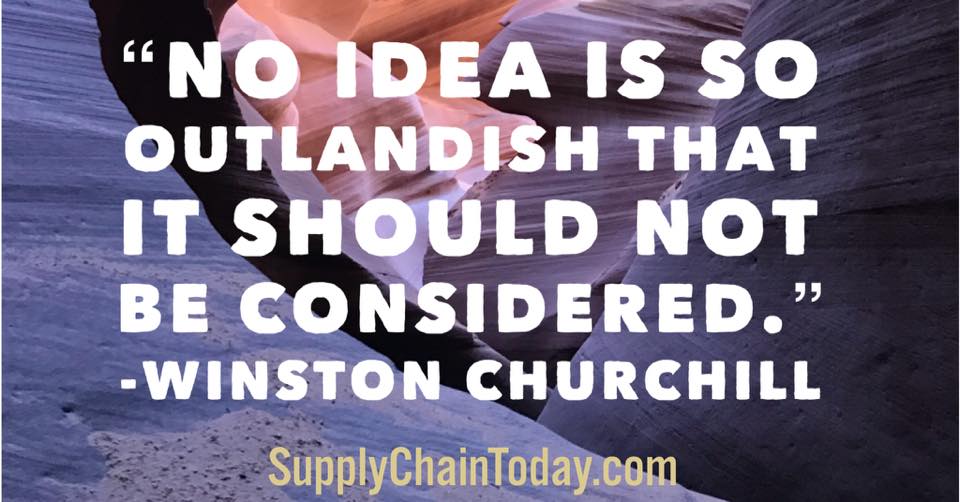
“Where there is no standard there can be no kaizen.” ~Taiichi Ohno, father of the Toyota Production System
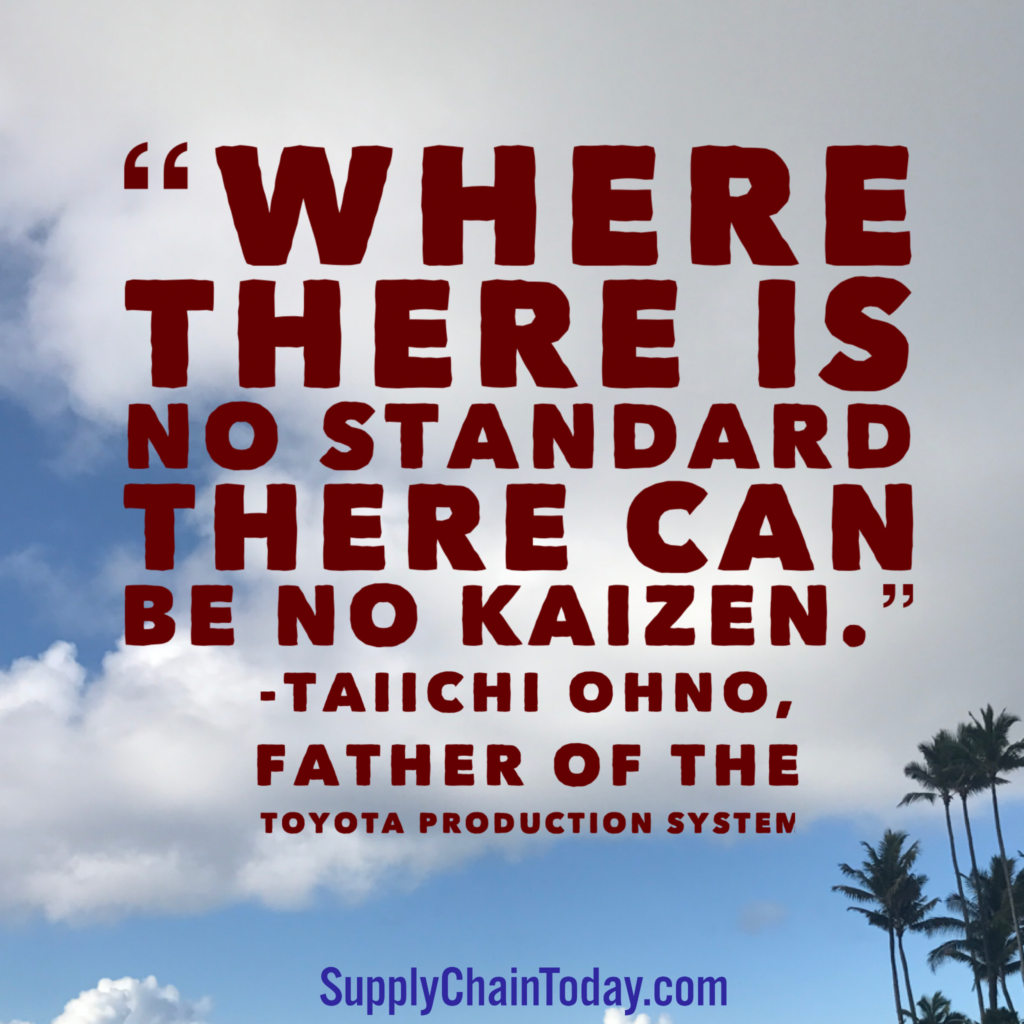
“Those in supply chain know the impossible is possible.”
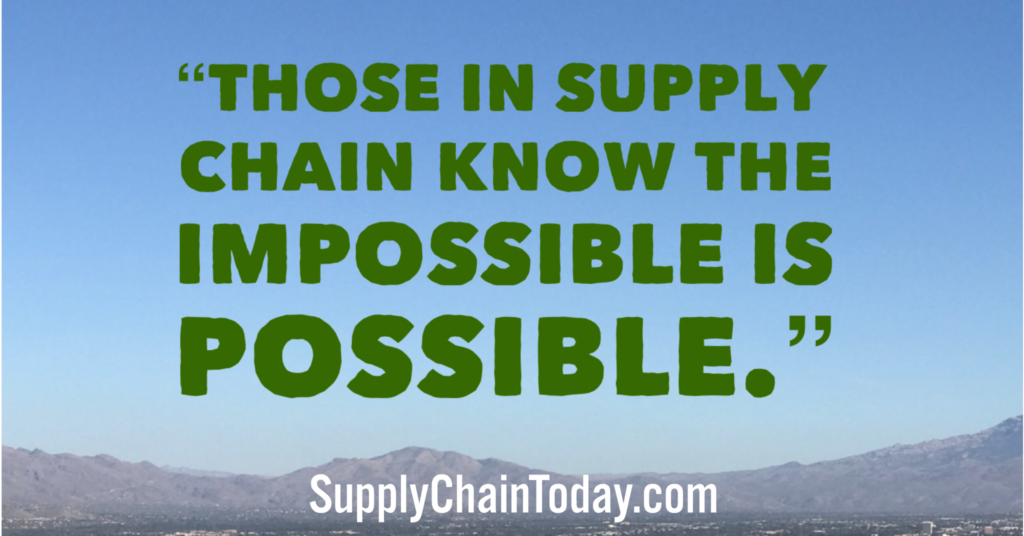
“99 percent of success is build on failure.” ~Charles Kettering
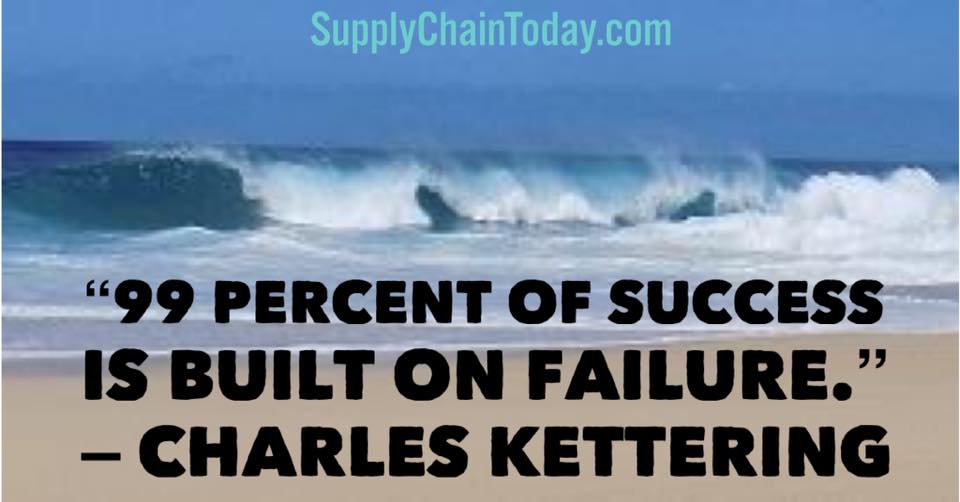
“Without change there is no innovation, creativity, or incentive for improvement. Those who initiate change will have a better opportunity to manage the change that is inevitable.” ~William Pollard
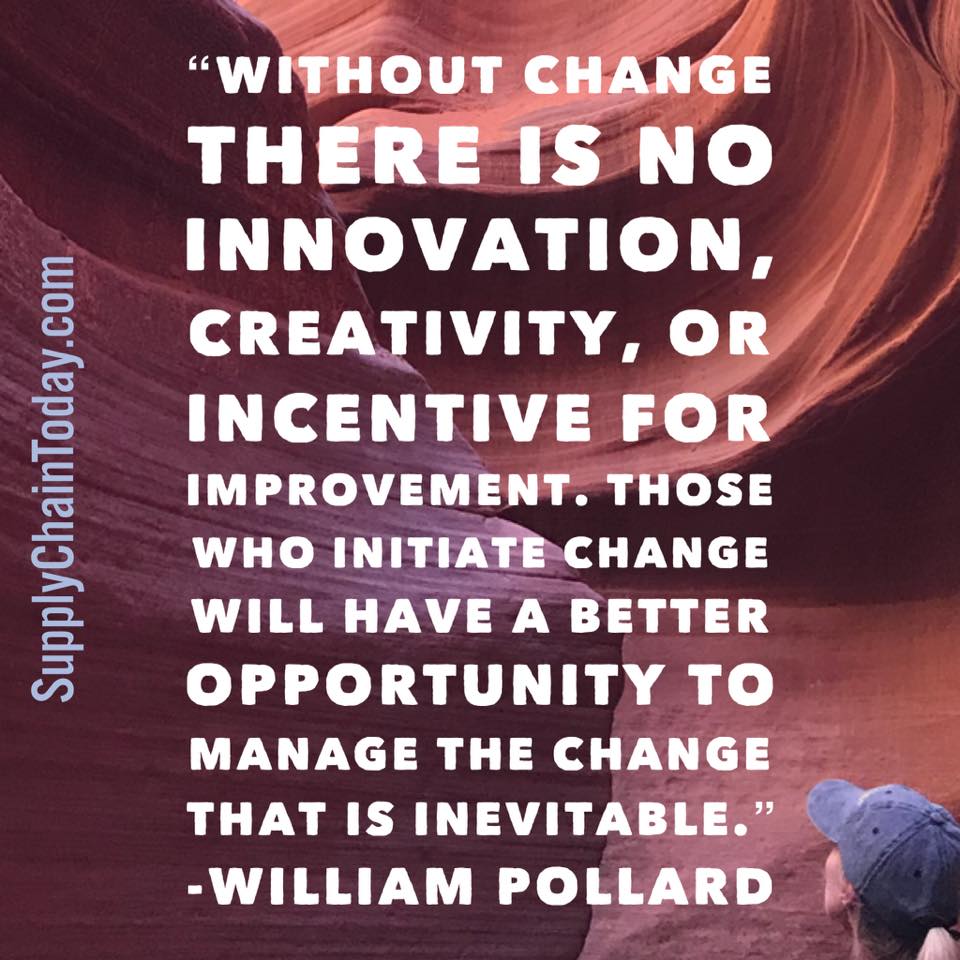