Lean Manufacturing – Pull Systems.
This is a four minute video on lean manufacturing pull systems. Great way to understand kanban and how to lean out supply chain.
Lean manufacturing pull systems are production systems in which production is triggered by customer demand rather than being based on a predetermined production schedule. In a pull system, production is “pulled” through the value stream by the customer, rather than being “pushed” through the value stream by the manufacturer.
Pull systems are designed to minimize waste and increase efficiency by only producing what is needed, when it is needed. This is in contrast to traditional “push” systems, in which production is based on forecasted demand, which can lead to excess inventory and waste if demand does not meet expectations.
Pull systems are typically implemented using a variety of techniques, including just-in-time (JIT) production, kanban systems, and constraint-based scheduling. These techniques are designed to minimize inventory levels and increase the speed and responsiveness of the production process.
Overall, lean manufacturing pull systems are a key component of lean manufacturing principles, which aim to minimize waste and increase efficiency in the production process.
Pros and Cons of Lean Manufacturing Pull Systems
Pros of lean manufacturing pull systems include:
- Reduced inventory levels, as products are only produced when there is demand for them
- Increased flexibility, as the system can quickly respond to changes in demand
- Improved quality, as products are only produced when there is a specific order for them
- Reduced lead times, as products are produced closer to the point of use
- Increased efficiency, as production is only initiated when there is actual demand for the product.
Cons of lean manufacturing pull systems include:
- It requires a high degree of coordination and communication among different departments
- It can be difficult to implement in industries with high variability in demand
- It can be difficult to implement in industries with long lead times for obtaining raw materials
- It requires a high level of trust between suppliers and manufacturers
- It may require significant changes to the existing production processes, which can be costly and time-consuming.
Cost Savings: Lean Pull Systems
The cost savings from lean manufacturing pull systems can be significant, and can come from a variety of sources. Some examples include:
- Reduced inventory costs: By only producing products when there is demand for them, companies can reduce the amount of inventory they need to hold, which can save money on storage, insurance, and handling costs. This can also lead to savings on the cost of capital, as less money is tied up in inventory.
- Reduced lead times: By producing products closer to the point of use, companies can reduce the lead times for delivering products to customers, which can save on transportation costs and improve customer satisfaction. This can also lead to reduced costs for expediting and airfreight, as well as improved on-time delivery performance.
- Increased efficiency: By only initiating production when there is actual demand for the product, companies can reduce the amount of waste and inefficiencies in their production process. This can lead to cost savings through reduced energy consumption, less scrap and rework, and improved machine utilization.
- Reduced scrap and rework: By producing products based on actual demand, companies can reduce the amount of scrap and rework generated by overproduction. This can lead to cost savings through reduced material and labor costs.
- Improved supplier relationships: By involving suppliers in the pull system, companies can build stronger relationships with their suppliers, which can lead to cost savings in the form of better prices and delivery times.
- Reduced downtime: By having production run at a steady pace, companies can reduce downtime caused by overproduction. This can lead to cost savings through increased productivity and reduced maintenance costs.
- Increased customer satisfaction: By producing products based on actual demand, companies can improve customer satisfaction by meeting their needs and reducing lead times. This can lead to cost savings through reduced returns, increased sales, and improved customer loyalty.
Lean and Continuous Improvement Quotes
- “Observing many companies in action, I am unable to point to a single instance in which stunning results were gotten without the active and personal leadership of the upper managers.” ~ Joseph M. Juran
- “Something is wrong if workers do not look around each day, find things that are tedious or boring, and then rewrite the procedures. Even last month’s manual should be out of date.” ~Taiichi Ohno
- “Learning is not compulsory; it’s voluntary. Improvement is not compulsory; it’s voluntary. But to survive, we must learn.” ~W. Edwards Deming
- “Without continual growth and progress, such words as improvement, achievement, and success have no meaning.” ~Benjamin Franklin
- “The most dangerous kind of waste is the waste we do not recognize.” ~Shigeo Shingo
- “The message of the Kaizen strategy is that not a day should go by without some kind of improvement being made somewhere in the company.” ~Masaaki Imai
- “The thing is, continuity of strategic direction and continuous improvement in how you do things are absolutely consistent with each other. In fact, they’re mutually reinforcing.” ~Michael Porter
Lean Manufacturing and Continuous Improvement Training
- Best Continuous Improvement Quotes.
- Deming, Juran and Crosby Quality Philosophies.
- John Shook Explains the Lean Transformation Model
- Kaizen – Toyota.
- Kanban explained in 60 seconds.
- Lean, Kaizen, and Continuous Improvement.
- Lean Manufacturing Quotes.
- Need Continuous Improvement Training? Try these resources.
- Process Improvement Quotes and Blogs.
- Process Improvement: Six Sigma & Kaizen Methodologies.
- Six Sigma In Plain English.
- The Kaizen Way: ONE SMALL STEP CAN CHANGE YOUR LIFE.
- Toyota Supply Chain Management.
Kaizen (Continuous Improvement): Secret behind Japanese Productivity
Toyota Production System Jidoka: Stopping Production, a Call Button and Andon.
The Best Continuous Improvement Quotes
What is Just in Time (JIT): Smartest Production System in The World
The Kaizen Way: ONE SMALL STEP CAN CHANGE YOUR LIFE
Dr. Deming Quotes – Continuous Improvement
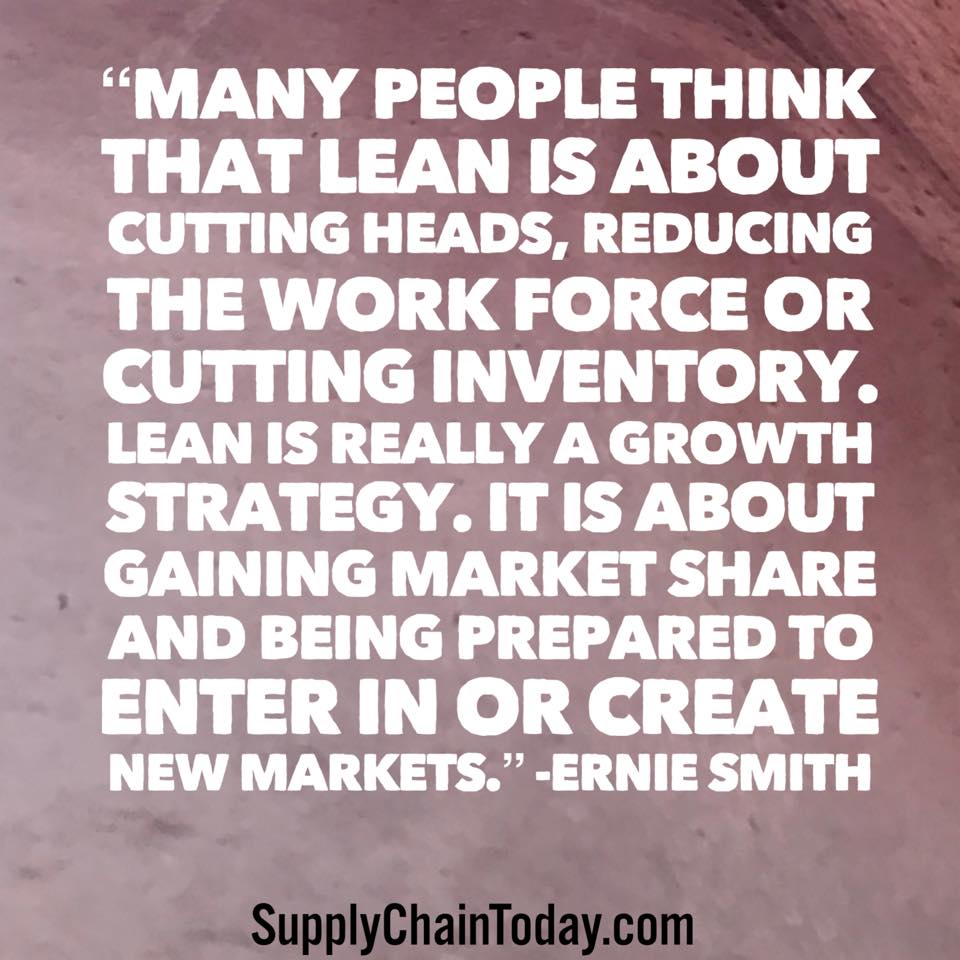