Gemba Walk: the Path to Continuous Improvement.
The Gemba Walk is walking around where the work is being done to understand what is going and and seeing how to help. It isn’t about seeing who is working, it is about seeing how you can make the workers life better so that they can be more efficient. Some may call this Management by Walking Around (MBWA). Lean principles are a great path to continuous improvement.
Here is further information on gemba:
Gemba is a Japanese term that means “the real place.” In the context of business and management, gemba refers to the location where value is created for customers. It is typically used in the context of lean manufacturing and continuous improvement, and it refers to the importance of going to the gemba to observe and understand the work processes and systems that are in place, in order to identify and eliminate waste and improve efficiency.
Gemba is often associated with the idea of “gemba walks,” which involve managers and leaders visiting the gemba to observe and understand the work processes and systems that are in place, and to identify opportunities for improvement. Gemba walks can be an effective way to identify problems and inefficiencies in the work environment, and they can help to generate ideas for improving processes and systems.
Gemba is an important concept in lean manufacturing and continuous improvement, and it emphasizes the importance of understanding and improving the work processes and systems that are in place in order to create value for customers.
The Importance of Doing Gemba
1. Gaining first-hand understanding: Seeing the process in person allows you to gather information and insights that wouldn’t be possible from data or reports alone. You can observe firsthand any problems, inefficiencies, or waste, and get a deeper understanding of the challenges faced by the people doing the work.
2. Connecting with employees: Gemba walks show employees that their work is valued and that you are interested in their input and suggestions. This fosters a sense of ownership and engagement, leading to a more collaborative and productive work environment.
3. Identifying opportunities for improvement: By observing the process firsthand, you can identify waste and inefficiencies that may not be readily apparent from data or reports. This allows you to make targeted improvements and optimize the process for greater efficiency and effectiveness.
4. Promoting continuous improvement: Gemba walks are a key component of the continuous improvement process. By regularly observing the process and identifying opportunities for improvement, you can create a culture of learning and innovation that drives long-term success.
5. Building trust and transparency: Gemba walks demonstrate a commitment to transparency and open communication. By going directly to the source of information, you can build trust with employees and stakeholders, and ensure that decisions are made based on accurate and up-to-date information.
Here are some additional benefits of doing Gemba:
- Increased problem-solving effectiveness: By seeing the problem firsthand, you can gain a better understanding of its root cause and develop more effective solutions.
- Improved decision-making: By gathering data and insights from the source, you can make more informed and data-driven decisions.
- Enhanced communication and collaboration: Gemba walks encourage cross-functional communication and collaboration between different departments.
- Boosted morale and motivation: Seeing management actively engaged in the work can motivate employees and improve morale.
Gemba and Continuous Improvement Quotes
- “People who can’t understand numbers are useless. The gemba where numbers are not visible is also bad. However, people who only look at the numbers are the worst of all.” ~Taiichi Ohno, father of the Toyota Production System
- “There are three kinds of leaders. Those that tell you what to do. Those that allow you to do what you want. And Lean leaders that come down to the work and help you figure it out.” ~John Shook
- “If you aren’t improving you are going out of business.” ~Dave Waters
- When you are out observing on the gemba, do something to help them. If you do, people will come to expect that you can help them and will look forward to seeing you again on the gemba. ~Taiichi Ohno
- “The frequency of leadership going to the Gemba is inversely proportional to the number of walls separating them from the Gemba.” ~Jon Miller
- “It’s pretty simple. If you have an environment where people aren’t afraid to speak up, and you listen to them things will get better.” ~Dave Waters
Lean and Continuous Improvement Training
- Agile Project Management with Kanban.
- Best Kaizen Quotes.
- Deming, Juran and Crosby Quality Philosophies.
- Deming’s 14 Points on Total Quality Management – TQM.
- Future Manufacturing: Toyota Innovation, Robotics, Artificial Intelligence.
- How to Deal with Change – Who Moved My Cheese?
- Kanban explained in 60 seconds.
- Lean Manufacturing – Lean Factory Tour – FastCap.
- Lean Six Sigma In 8 Minutes.
- Process Improvement Quotes and Blogs.
- Process Improvement: Six Sigma & Kaizen Methodologies.
- Six Sigma In Plain English.
- Space Shuttle Challenger Disaster and Supply Chain Issues.
- Supply Chain Resources by Topic & Supplier.
- The Best Continuous Improvement Quotes.
- TOYOTA Production System: Kanban Production.
- What is CHANGE MANAGEMENT?
Toyota Production System Jidoka: Stopping Production, a Call Button and Andon.
The Best Continuous Improvement Quotes
What is Just in Time (JIT): Smartest Production System in The World
The Kaizen Way: ONE SMALL STEP CAN CHANGE YOUR LIFE
Dr. Deming Quotes – Continuous Improvement
Lean Manufacturing | A pursuit of perfection.
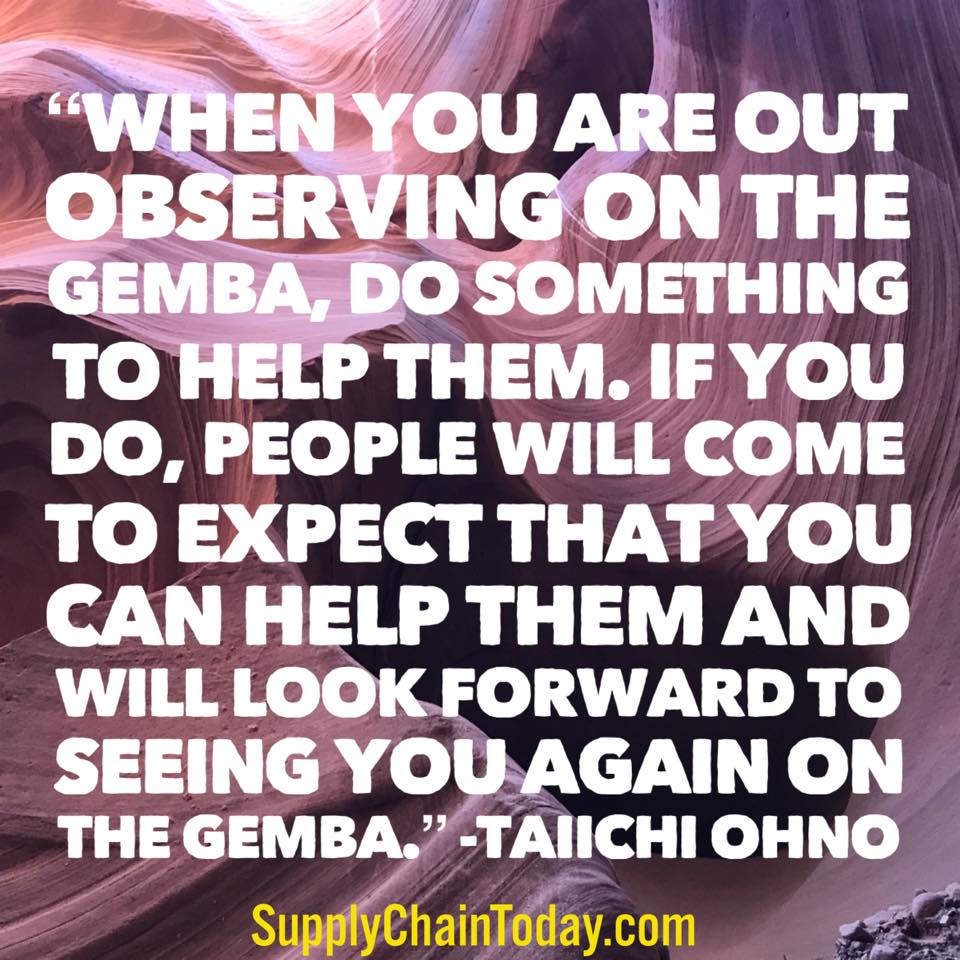