Lean Concepts WWII – Continuous Improvement by People Doing the Work.
This is a quick one minute video that packs a punch to convince leadership to act on continuous improvement and get the people doing the work involved. This isn’t a new concept. We use a poster from World War II to show it isn’t a new concept. This has been around for a long time. You don’t need to be an expert in continuous improvement to get the ball rolling. If your company isn’t getting the people involved doing the work then it is basically saying your leadership style is pre 1940s. A little bit of sarcasm there but hopefully that will get people to think.
Lean Concepts
Lean concepts, often associated with the Toyota Production System, were not formally developed until after World War II, but some of the principles and practices that later became integral to lean manufacturing were indeed used during the war, particularly by the United States. The need for efficient and effective production methods in wartime led to the adoption of many practices that aligned with lean thinking. Here are some ways in which lean concepts were applied during World War II:
- Standardization: To streamline production and reduce complexity, standardization of parts and components was critical during the war. Standardizing items reduced the need for various versions and made it easier to replace damaged equipment or vehicles.
- Just-in-Time (JIT): JIT principles involve producing and delivering products or components just in time to meet demand while minimizing excess inventory. In World War II, the U.S. military implemented JIT practices to ensure that supplies and equipment were available when and where they were needed, reducing excess stockpiles and waste.
- Pull Systems: Pull systems are a fundamental aspect of lean manufacturing, where production is driven by actual customer demand. During the war, various supply chains adopted pull systems to replenish materials and equipment as needed, rather than pushing products into the system without regard to demand.
- Kaizen (Continuous Improvement): While not formally called “kaizen,” the idea of continuous improvement was important during the war. Military and industrial leaders recognized the need to constantly assess and refine processes to optimize efficiency and effectiveness.
- Waste Reduction: Lean principles emphasize eliminating waste, and this was crucial during World War II. The military and industries made efforts to reduce various forms of waste, including overproduction, excess inventory, defects, and underutilized worker skills.
- Cross-Training: To ensure flexibility and adaptability, workers were often cross-trained to perform multiple tasks, much like the lean concept of multi-skilling to address labor shortages or bottlenecks.
- Value Stream Mapping: Though not as formalized as in modern lean practices, value stream mapping was implicitly used to assess and improve processes, especially in wartime production lines and logistics.
It’s important to note that the formalization and comprehensive development of lean principles, as we know them today, came after World War II through the efforts of Toyota and other organizations in post-war Japan.
Quotes from Great Minds
- “The competitor to be feared is one who never bothers about you at all, but goes on making his own business better all the time.” ~Henry Ford, founder of Ford Motor Company
- “It’s our job every day to make every important aspect of the customer experience a little bit better.” ~Jeff Bezos, founder of Amazon
- “The widespread availability of information is the only basis for effective day-to-day problem solving, which abets continuous improvement programs.” ~Tom Peters
- “The most dangerous kind of waste is the waste we do not recognize.” ~Shigeo Shingo
- “Unless you continually work, evolve, and innovate, you’ll learn a quick and painful lesson from someone how has.” ~Cael Sanderson, Olympic Gold Medalist
- “I probably have traveled and walked into more variety stores than anybody in America. I am just trying to get ideas, any kind of ideas that will help our company. Most of us don’t invent ideas. We take the best ideas from someone else.” ~Sam Walton, founder of Walmart
- “The Hacker Way is an approach to building that involves continuous improvement and iteration. Hackers believe that something can always be better, and that nothing is ever complete.” ~Mark Zuckerberg, founder and CEO of Facebook
Continuous Improvement Training
- All About Value Stream Mapping.
- Continuous Improvement – The Most Important Aspect… START.
- History of Continuous Improvement & Quality Gurus
- Lean Manufacturing Quotes.
- Lean Six Sigma In 8 Minutes.
- Process Improvement: Six Sigma & Kaizen Methodologies.
- Pull Systems: Lean Manufacturing.
- The Best Continuous Improvement Quotes
- The Path to Success with Paul Akers: Lean Manufacturing
Toyota Production System Jidoka: Stopping Production, a Call Button and Andon.
The Best Continuous Improvement Quotes
What is Just in Time (JIT): Smartest Production System in The World
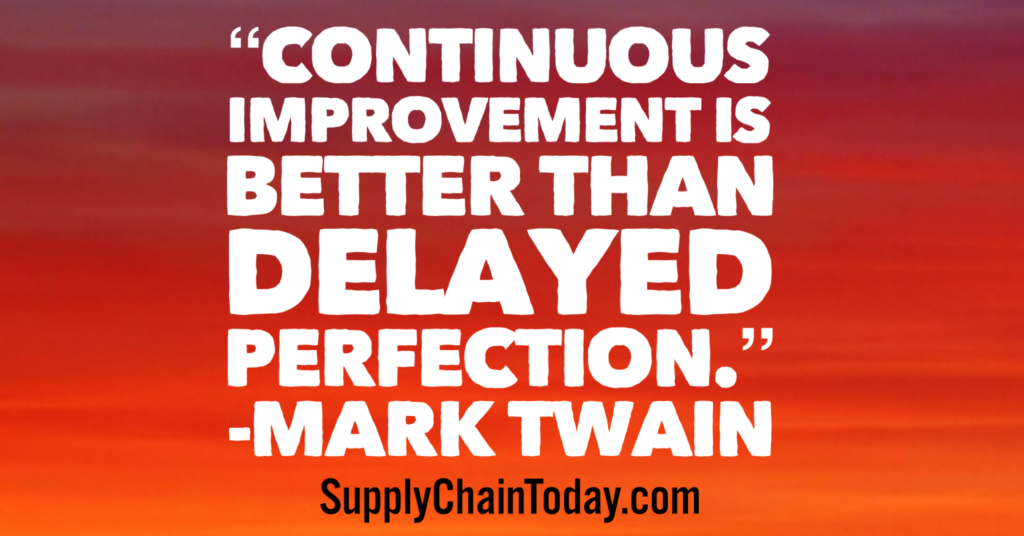