What is Industry 4.0.
Industry 4.0, also known as the Fourth Industrial Revolution, refers to the integration of advanced technologies, such as artificial intelligence, the Internet of Things (IoT), and automation, into industrial processes. These technologies have the potential to fundamentally change the way that supply chains are managed.
Some ways in which Industry 4.0 is expected to change supply chain management include:
- Increased automation: The use of advanced technologies, such as robotics and IoT, can enable increased automation of supply chain processes. This can lead to increased efficiency and productivity, as well as reduced costs.
- Improved decision-making: Industry 4.0 technologies, such as artificial intelligence and machine learning, can provide supply chain managers with real-time data and analytics, which can be used to make more informed decisions about logistics and operations.
- Enhanced visibility and traceability: The use of advanced technologies, such as blockchain, can provide a detailed and transparent record of supply chain processes, which can help to increase visibility and traceability.
- Greater agility and responsiveness: Industry 4.0 technologies can enable supply chain managers to quickly and easily adapt to changing customer demand and market conditions.
Overall, Industry 4.0 is expected to fundamentally change the way that supply chains are managed, through the integration of advanced technologies, such as artificial intelligence, the Internet of Things, and automation. These technologies have the potential to increase automation, improve decision-making, enhance visibility and traceability, and increase agility and responsiveness in supply chain management.
Pros and Cons of Industry 4.0
Some potential advantages of Industry 4.0 include:
- Increased efficiency: Automation and data analysis can help optimize production processes, reducing waste and increasing productivity.
- Improved quality: By collecting data on every aspect of production, it is possible to identify and address problems more quickly, leading to a reduction in defects.
- Enhanced flexibility: With the ability to quickly reconfigure production lines and adapt to changing customer demands, Industry 4.0 can help businesses respond more nimbly to market changes.
- Greater transparency: By gathering and analyzing data on all aspects of production, it is possible to gain a more complete understanding of how a business is operating, which can facilitate better decision-making.
Some potential disadvantages of Industry 4.0 include:
- Cost: Implementing Industry 4.0 technologies can be expensive, and small businesses may struggle to afford the necessary investments.
- Skills gap: There may be a shortage of workers with the necessary skills to work with Industry 4.0 technologies, which could limit the adoption of these technologies.
- Security risks: The increased use of connected devices and data exchange introduces new security risks, such as the possibility of cyber attacks.
- Job displacement: Automation and data analysis can potentially lead to job displacement, as some tasks may be taken over by machines. This could lead to social and economic disruption.
Cost Savings: Industry 4.0
- Increased efficiency: By automating tasks and optimizing production processes, businesses can reduce waste and increase productivity, which can lead to cost savings.
- Reduced defects: By collecting data on every aspect of production, it is possible to identify and address problems more quickly, leading to a reduction in defects and resulting cost savings.
- Better resource utilization: Industry 4.0 technologies can help businesses better understand and manage their resources, leading to more efficient use of materials and energy.
- Improved maintenance: Help businesses identify potential issues before they occur, allowing for timely repairs and preventing costly breakdowns.
- Reduced waste: By using data analysis to optimize production processes, businesses can reduce the amount of waste generated, leading to cost savings.
- Enhanced supply chain management: Help businesses improve their supply chain management, leading to more efficient and cost-effective operations.
Industry 4.0: The Future of Manufacturing
Further Information on Industry 4.0.
Industry 4.0, also known as the Fourth Industrial Revolution, is the current trend of automation and data exchange in manufacturing technologies and processes. It includes cyber-physical systems, the Internet of Things (IoT), cloud computing, and cognitive computing.
Industry 4.0 is characterized by the convergence of information technology (IT) and operational technology (OT). IT refers to the software and hardware that businesses use to manage their operations, while OT refers to the physical devices and systems that control the production process.
The convergence of IT and OT is made possible by the development of new technologies, such as:
- Cyber-physical systems (CPS): CPS are physical systems that are embedded with sensors and software that allow them to collect and exchange data.
- The Internet of Things (IoT): The IoT refers to the network of physical devices that are connected to the internet. These devices can collect and exchange data, which can be used to improve efficiency and productivity.
- Cloud computing: Cloud computing refers to the delivery of IT services over the internet. This allows businesses to access computing power and storage on demand, which can help to reduce costs and improve scalability.
- Cognitive computing: Cognitive computing refers to the use of artificial intelligence (AI) and machine learning to mimic human thought processes. This can be used to automate tasks, improve decision-making, and discover new insights.
Benefits
- Increased efficiency: By automating tasks and using data analytics, businesses can improve efficiency and reduce costs.
- Improved quality: By monitoring and controlling the production process, businesses can improve quality and reduce defects.
- Increased flexibility: By making it easier to change production lines, businesses can respond more quickly to changes in demand.
- Reduced environmental impact: By optimizing the production process, businesses can reduce their environmental impact.
- Enhanced worker safety: By automating dangerous tasks, businesses can improve worker safety.
Challenges:
- High cost of implementation: The cost of implementing Industry 4.0 technologies can be high, especially for small businesses.
- Security concerns: The interconnected nature of systems makes them vulnerable to cyberattacks.
- Skills gap: There is a shortage of skilled workers who are able to implement and use Industry 4.0 technologies.
- Regulatory challenges: There are a number of regulatory challenges that businesses need to consider when implementing technologies.
Despite the challenges, Industry 4.0 is a promising field with the potential to revolutionize the manufacturing industry. Businesses that are able to adopt these technologies early can gain a competitive advantage.
Industry 4.0 Resources
High-tech Production Without People | Industry 4.0Â
Dark Factory – Automated Factory with Minimal Human Involvement.
Spot doing Autonomous Inspections at the Nestlé Purina Factory.
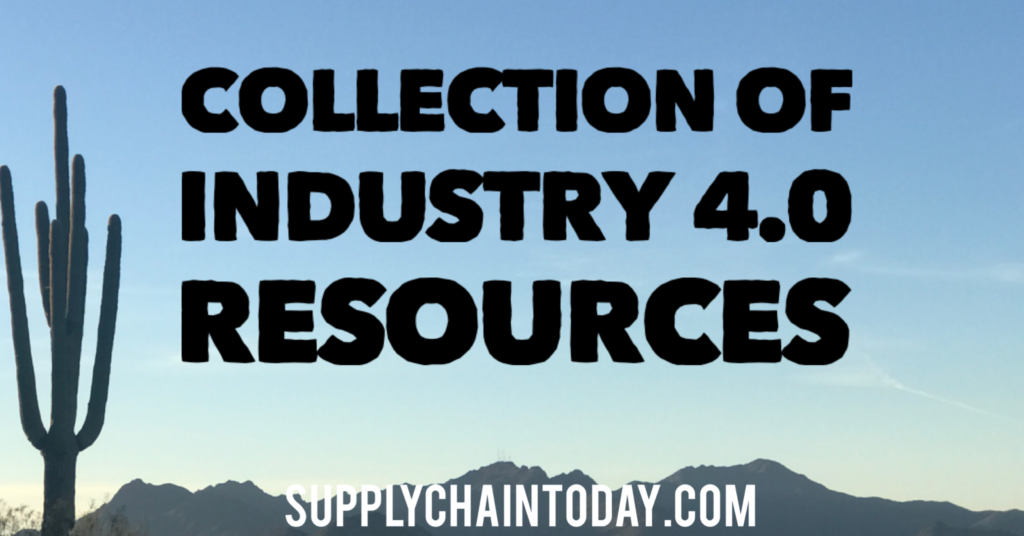